Transforming Pet Food Quality, One Bite at a Time
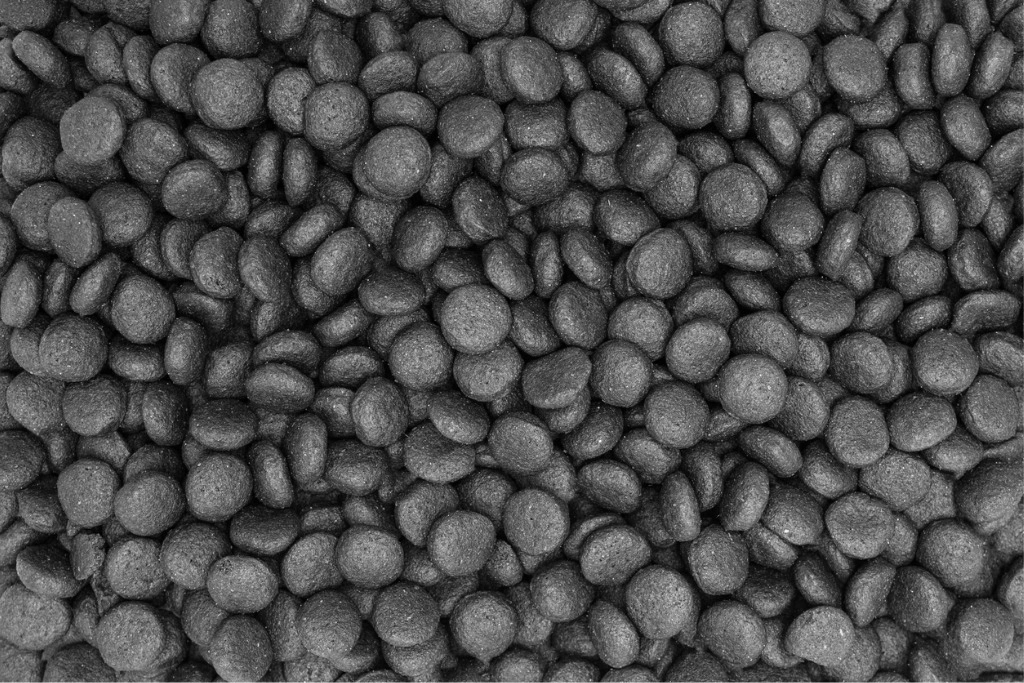
In homes across America, where two-thirds of households include a pet, these animals are more than just animals; they're part of the family. And like any loved one, they deserve the very best when it comes to their diet. Choosing a pet food brand is a big deal—it means trusting someone else to care for your pet as much as you do, ensuring every meal is safe and full of the good stuff. That’s a big ask, and pet food makers feel the weight of that trust every day.
At Gray Solutions, we get how important this is. Our expert team, loaded with some of the best minds in automation and vision tech, has taken pet food quality control (QC) to the next level for the biggest names and the niche players in pet food. We’re all about pushing the boundaries, using our drive for innovation to make sure your pet's food is as perfect as it can be. We're here to make a difference, transforming the norm and setting new standards for what pet food quality looks like.
Revolutionizing Quality Control with Human-Robot Synergy
When processing dog kibble, moisture content is a bit of a Goldilocks metric. Too much moisture and you could have mold issues once the food is packaged. Too little moisture and the product won’t be dense enough, leading to kibble that may be unpalatable. To guarantee moisture content is just right, you need to sample kibble during processing and quickly make adjustments if target values are not being met. When this process is done manually, it can take 30 – 45 minutes to see results, giving lots of time for more over-dried kibble to come down the line.
Tackling palatability issues, frequently spotlighted through customer insights and feedback, the R&D team at a leading U.S. pet food innovator uncovered a tendency to over-dry kibble. This challenge, typically unnoticed in-house until the final product stages, was also stirring up density dilemmas during packaging.
That’s where we stepped in, introducing automation into the mix with QC cobots. These aren’t your everyday robots; they’re equipped with safety features that let them work right alongside people without a hitch. The cobots have cutting-edge vision systems and near-infrared (NIR) technology, making them capable of inspections at a speed and precision that’s simply out of reach for human operators.
One cobot lives at the top of the customer’s eight-story dryer stack while the other lives at the bottom. Up high, each batch of kibble undergoes a meticulous check—weighed, captured in a time-stamped 2D photo, and scanned in 3D to assess its volume. Down below, the kibble faces another round of weighing to ensure consistency. Right on the production line, it's as if a mini lab springs into action: samples are transformed into a fine powder and analyzed using near-infrared (NIR) technology. And it doesn't stop there; another time-stamped 2D photo is taken, bolstering traceability and offering insight into the inspection frequency for each batch.
Then, the system swiftly crunches the numbers against the key performance indicators (KPIs) that matter. It's smart enough to tweak the drying process in real-time, aiming for that sweet spot every time. With automation, we've cut down the wait—gone are the days of twiddling thumbs waiting for sample analysis before making necessary tweaks. The result? Pure efficiency =perfectly dried kibble without the extra cost.
Building a Future-Proof Quality-Centric Facility
When another top-tier pet food maker in the U.S. decided to ramp up their game by doubling the production of their specialty wet food, they were adamant that quality wasn’t just a feature but the foundation of their new facility. With our parent company, Gray, at the helm of developing this state-of-the-art smart factory, we were tapped for our automation prowess. Our mission? To weave smart technologies throughout the fabric of the plant, guaranteeing that every drop morsel of wet food meets the gold standard for quality and food safety, without fail.
Boosting quality to the next level meant diving deep into every nook and cranny of production and automation. At the heart of this operation sits a cutting-edge mission control room, serving as the nerve center of the entire facility. This hub offers a panoramic view of the production process, giving stakeholders a clear window into every phase—from initial ingredient intake through final packaging. And it’s not just about oversight from the center; operators across the plant are armed with tablets, enabling them to keep a pulse on operations and manage controls right from the factory floor.
We also strategically included multiple product inspection and verification points throughout the manufacturing process. Vision-based inspection systems operate alongside expertly trained QC staff to ensure products are meeting internal and external quality standards and protocols. And we dialed up the digital technology used for double and triple-checking critical steps in the production process such as performing batch verification to confirm the correct raw materials, in the correct quantities, were used.
Redefining Premium Pet Food Production
If you’re in the business of creating top-notch pet food, earning and keeping consumer trust is everything. That’s why, when an international leader in premium pet food decided to set up its very first U.S. plant, the company teamed up with us. Our goal? Creating a plant that would be the envy of top food processors everywhere.
To optimize quality measures, we incorporated automated continuous monitoring systems at various points in the production process. Every bit of cooking data, from the get-go to the final dish, gets sent straight to these systems and laid out live for the kitchen control team. This setup lets our operators keep a keen eye on every step, spotting and stopping potential issues in their tracks. With quality as our guiding star from start to finish, we also set up an automated clean-in-place (CIP) system that ensures the proper time, temperature, and turbulence is used for cleaning equipment between batches. Because this award-winning facility was such a success, a few years later we were contracted to use our same approach to build a new Canadian facility as well.
Looking to beef up your pet food processing quality measures? In addition to our world-class automation experts, our team also includes food safety specialists and Solutioneers with in-the-trenches pet food processing experience. We are the experts in pet food automation. Think you have a challenge we can’t solve? Talk to one of our Solutioneers today.